I remember the early years of production when we sought a manufacturing license and visited the Planning and Development Department at the Ministry of Industries. This department had comprehensive statistics on industrial production across various sectors in Iran, providing us with valuable and useful information. Unfortunately, this system has now been completely dismantled, and nowadays, people establish factories without proper research, planning, or knowledge of the number of existing factories and similar productions. I suggest that this sector of the industry (nonwoven textiles) should receive more attention from the Ministry of Industries and Mines, as well as other relevant authorities.
In the past, there were very few nonwoven manufacturing factories in Iran, and no official statistics were available. The first Bibaf factory for producing thermobonded interlining was established in 1982. At that time, only two factories, Nobaf and Iran Laei, were producing nonwoven textiles in the fields of needle punch and spray-bonded interlining. Back then, the nonwoven textiles market was thriving. However, as miscellaneous factories began to emerge, within 4 to 5 years, the number of these factories grew from just a few to over 50 nonwoven manufacturing units, and this upward trend continues to this day.
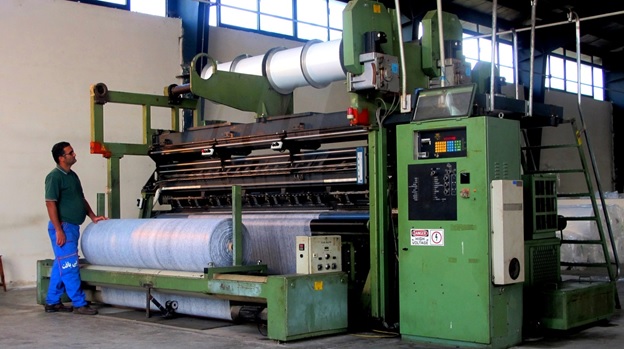
On one hand, some factories have shut down due to economic challenges, while on the other hand, new factories are being established without proper research and planning. As a result, these factories often end up copying each other’s production, leading to financial losses. Currently, the number of interlining manufacturing factories has grown so much that the selling prices are not reasonable at all. If this investment were directed towards other ventures, it would likely yield far higher returns than producing nonwoven textiles.
Most existing factories have set up their production lines by securing loans and importing outdated machinery, which has either led them to halt production due to poor market conditions or forced them to sell their equipment. For example, many waterproofing membrane (bituminous membrane) factories, facing the daily rise in interlining prices, have set up their own carding, feeding, and needle punching lines in-house. It is no longer cost-effective for them to purchase interlining from another company, which in turn has led to a market slump.
Final Thoughts?
In my opinion, the survival of factories like ours heavily depends on governmental policies. There was a time when, due to favorable market conditions, the income per capita of factories was significant, leading to a high volume of sales for items like shoes, clothing, and more. However, today, the income of the middle class has dropped so drastically that clothing is no longer a priority for families, with most of their spending directed toward food and daily expenses. Unfortunately, this trend continues.
Despite warnings from the Textile Industry Syndicate and industry stakeholders to the authorities regarding the declining presence of this sector in production, as well as challenges related to insurance costs, taxes, electricity, gas, check laws, and labor regulations—which have slowed down production and, in the end, led to factory closures—no action has been taken. Instead, the facilities provided for importing goods, such as tariff adjustments, have contributed to the decline of this industry. Banking facilities like loans do not solve the underlying issues of this sector, as the lack of profitability in the production cycle leads recipients to use these loans for other purposes, such as construction, rather than reinvesting them into production.
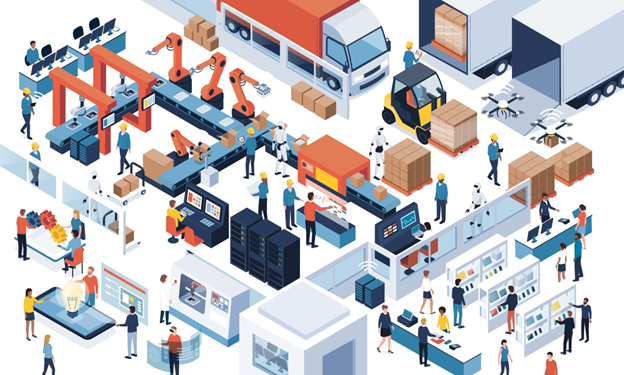
Factories have been left to fend for themselves. The survival of factories like ours depends heavily on government policies. There was a time when, thanks to favorable sales conditions, factory incomes were significant, leading to a high volume of sales in shoes, clothing, and more. However, today, the income of the middle class has declined so much that clothing is no longer a priority for families, with most of their spending directed toward food. Unfortunately, this trend continues.
In recent years, our production capacity has dwindled, our workforce has decreased, and if this trend continues, production will gradually come to a halt. We have invested all our resources into production to keep the factory and manufacturing running, which means our survival is tied to the government’s macroeconomic policies. Chinese imported goods are often of low quality (grades 3 and 4), but if high-grade Chinese products are imported, you will find that they are much more expensive than our products. Believe me, Iranian-made products have very good quality in many areas. Ensuring the survival of manufacturing plants like ours should be a top priority for the government. Although the influx of Chinese imports has caused issues in other markets as well, these countries have regulated imports to meet their quality standards. If high-quality Chinese products enter our market properly and according to standards, we also have standards in place. However, due to many existing challenges, these standards are not always followed. If standards were strictly enforced, the price of Chinese products would far exceed that of domestic goods. Thus, we are entirely dependent on government policies to control imports, as unchecked imports gradually undermine local production.
Foreign companies, one after another, are refusing to accept Iranian letters of credit, making it difficult for factories to procure raw materials. Many companies no longer sell spare parts for factory machinery to Iran due to the current conditions, forcing factories to find alternative methods to import them at a higher cost. Power fluctuations damage the electronic boards of machines, requiring replacements each month. Given the current situation, importing these components has become increasingly difficult. Electricity costs are also rising annually, with no attention paid to these losses. If the electricity bill is even slightly delayed, there are threats to cut off the factory’s power.
After bearing the high costs, we converted all the factory’s systems from diesel to gas in 2007, feeling optimistic about starting the year without fuel issues. However, in the current situation, the factory’s gas supply has been entirely cut off for six weeks, forcing us to stop some production lines. As a result, at the end of this challenging year, we have been compelled to lay off staff and reduce working hours. To keep the factory running and provide heating in the halls, we had to convert the burners back from gas to diesel, but the high costs prevented us from fully completing this transition. We sincerely extend our hands to the authorities, asking them to address the dire situation of the textile industry. No factory wants to dismiss its workers—employees are the heart of the factory—but under the current circumstances, for the factories to survive, layoffs have become inevitable.